Each year at Washington State University in Pullman, Washington, the Formula SAE (Society of Automotive Engineers (SAE) team builds a formula style race car from the ground up. The team designs, constructs, and tests the car with the ultimate goal of using it to compete against other Formula SAE teams from universities around the world.
The Formula SAE-Society of Engineers--team discovered an available shop on campus and jumped at the opportunity to create a composites fabrication shop. There, they were able to build the composite body, seat, steering wheel, pedals, and other materials for their car. The mixing of resins such as epoxy is a critical aspect of the composite creation process. In order to ensure the quality of the epoxy, it is critical to mix it to the correct ratio in order to avoid an improper cure and lower mechanical properties for the part. In order to ensure the effectiveness - and safety - of the car's parts, making sure their ratios are correct in the mixing process is critical.
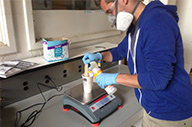
Mixing epoxy by weight produces the most accurate results and that is why the school's Formula SAE team turned to OHAUS Corporation in order to identify the right scale for their needs. With their limited budget in mind, OHAUS donated a Ranger 3000 compact bench scale to the school. The scale is ideal for their needs as it has a high capacity and high resolution. Typical batches of resin can weigh up to 10 kg but also need to be accurate down to 1g.
"Most scales with high resolution seem to also have a low capacity, so the Ranger 3000 scale is beneficial to us because it has high resolution and high capacity," said David Lemme, the team's composite lead.
The first step in designing this year's racer is to create the car's body with a block of foam, then fabricate a composite tool off of it in order to build the body from the composite tool.
"Ranger 3000 will certainly increase the accuracy of our epoxies which will lead to stronger parts, but it also makes the process of mixing epoxy easier and safer," said Lemme. "Having a reliable scale with a high capacity does not restrict us to making small batches only."
The Formula SAE team has agreed to open the composite fabrications shop to other clubs and on campus. The shop, only in its first year, has already garnered interest from the school's electrical vehicle club and American Institute of Aeronautics and Astronautics club, as well as senior design students whose senior projects would benefit from the use of the composites fabrication shop.
"The knowledge that our new shop has quality equipment such as the Ranger 3000 should really generate increased interest when we gear up in the fall," said Lemme. "Knowing that we have the ability to accurately mix resins right here on campus will be a big draw."
Learn more about the
Ranger® 3000